JIS G3462 Alloy steel tubes for boiler and heat exchanger
JIS G 3462
Alloy steel tubes for boiler and heat exchanger
1 Scope
This Standard specifies the alloy steel tubes (hereafter referred to as "tubes") used for exchanging heat between the inside and outside of the tube, such as water tubes,smoke tubes, superheater tubes and air preheater tubes of boilers, and heat exchanger tubes, condenser tubes and catalyst tubes used in chemical and petroleum industries.It is not applicable to the steel tubes for heating furnace and steel heat exchanger tubes for low temperature service .
This Standard applies to tubes with an outside diameter of 15.9 mm. to 139.8 mm.
With the preyious agreement of the manufacturer, the purchaser may designate the special quality requirements and designate U-bend tubes to be applied,given in Annex JA and Annex JBA respectively in addition to the requirements specified .in the. text of this Standard.
NOTE: The International Standards corresponding to this Standard and the symbol of degree of correspondence are as follows:
ISO 9329-2 : 1997 Seamless steel tubes for pressure purposes - Technical delivery conditions - Part 2 : Unalloyed and alloyed steels with specified eleva ted tempera ture properties ISO 9330-2 : 1997 Welded steel tubes for pressure purposes - Technical delivery conditions - Part 2 : Electric resistance and induction welded unalloyed and alloyed steel tubes with specified elevated temperature properties (overall evaluation: MOD)The symbols which denote the degree of correspondence in the contents between the relevant International Standards and JIS are IDT (identical), MOD (modified), and NEQ (not equivalent) according to ISO/lEe Guide 21-1.
2 Normative references
The following standards contain provisions which, through reference in this text,constitute provisions of this Standard. The most recent editions of the standards (including amendments) indicated below shall be applied.
JIS G 0320 Standard test method for heat analysis of steel products
JIS G 0321 Product analysis and its tolerance for wrought steel
JIS G 0404 Steel and steel products - General technical delivery requirements
JIS G 0415 Steel and steel products - Inspection documents
JIS G 0416 Steel and steel products - Location and preparation of samples and test pieces for mechanical testing
JIS G 0567 Method of elevated temperature tensile test for steels and heat-resisting alloys
JIS G 0582 Automated ultrasonic examination of steel pipes and tubes
JIS G 0583 Automated eddy current examination of steel pipes and tubes
JIS Z 2241 Metallic materials - Tensile testing - Method of test at room temperature
JIS Z 2245 Rockwell hardness test - Test method
JIS Z 8401 Guide to the rounding of numbers
3 Classification and symbols
Tubes shall be classified into grades, and the designation of grade and designation of manufacturing method shall be as given in table 1
Table 1 Designation of grade, designation of manufacturing method and marking
Designation of grade | Designation of manudacturing method | |||
Tube manufacturing method | Finishing method | Marking | ||
Molybdenum steel tube | STBA12 |
Seamless: S Electric resistance welded: E |
Hot finished: H Cold finished : C As electric resistance welded: G |
Designation of manudacturing method shall be in accordance with 12 b). |
STBA13 | ||||
Chromium -molybdenum steel tube | STBA20 | |||
STBA22 | ||||
STBA23 | ||||
STBA24 | ||||
STBA25 | Seamless: S |
Hot finished: H Cold finished : C |
||
STBA26 |
4. Manufacturing method
The manufacturing method shall be as follows.
(a)Tubes shall be manufactured by a combination of the manufacturing method and finishing method given in table 1
(b)The tubes of STBA 12, STBA 13, STBA 20 and STBA 22 shall be manufactured by seamless process or by electric resistance welding process and the tubes of STBA 23, STBA24, STBA 25 and STBA 26 shall be manufactured by seamless process.
(c)Tubes shall be subjected to the Heat treatment specified in table 22.Other heat treatments not specified in table 2 shall be agreed between the purchaser and the manufacturer.
(d) Plain end finishing shall be applied to the shape of tube end unless otherwise specified.
Table 2 Heat treatment
Designation of grade | Heat treatment a) |
STBA12 STBA13 |
Low temperature annealing, isothermal annealing, full annealing,normalizing or normalizing followed by tempering |
STBA20 STBA22 |
Low temperature annealing, isothermal annealing, full annealing or normalizing followed by tempering |
STBA23 STBA24 STBA25 STBA26 |
Isothermal annealing, full annealing or normalizing followed by tempering b) |
Notes a) Low temperature annealing shall not be applied to the electric resistance welded steel tube. b)The tempering temperature for STBA 23, STBA 24, STBA 25 and STBA 26 shall be 650°C or higher. |
5. Chemical composition
Tubes shall be tested in accordance with 10.1 and the heat analysis value shall conform to table 3. As required, alloy elements not included in table 3 may be added.
When the product analysis is required by the purchaser, tubes shall be tested in accordance with 10.1 and the product analysis value shall conform to table 3.
Table 3 Chemical composition
Standard | Grade | Chemical Composition Limits (%) | ||||||
C | Si | Mn | P | S | Cr | Mo | ||
JIS G3462 | STBA12 | 0.10-0.20 | 0.10-0.50 | 0.30-0.80 | ≤ 0.035 | ≤ 0.035 | - | 0.45-0.65 |
STBA13 | 0.15-0.25 | 0.10-0.50 | 0.30-0.80 | ≤ 0.035 | ≤ 0.035 | - | 0.45-0.65 | |
STBA20 | 0.10-0.20 | 0.10-0.50 | 0.30-0.60 | ≤ 0.035 | ≤ 0.035 | 0.050-0.080 | 0.45-0.65 | |
STBA22 | ≤ 0.15 | ≤ 0.50 | 0.30-0.60 | ≤ 0.035 | ≤ 0.035 | 0.80-1.25 | 0.45-0.65 | |
STBA23 | ≤ 0.15 | 0.50-1.00 | 0.30-0.60 | ≤ 0.030 | ≤ 0.030 | 1.00-1.50 | 0.45-0.65 | |
STBA24 | ≤ 0.15 | ≤ 0.50 | 0.30-0.60 | ≤ 0.030 | ≤ 0.030 | 1.90-2.60 | 0.87-1.13 | |
STBA25 | ≤ 0.15 | ≤ 0.50 | 0.30-0.60 | ≤ 0.030 | ≤ 0.030 | 4.00-6.00 | 0.45-0.65 | |
STBA26 | ≤ 0.15 | 0.25-1.00 | 0.30-0.60 | ≤ 0.030 | ≤ 0.030 | 8.00-10.00 | 0.90-1.10 |
6 .Mechanical properties
6.1 Tensile strength, yield point or proof stress, and elongation
Tubes shall be tested in accordance with 10.2.3, and the tensile strength, yield point or proof stress, and elongation shall conform to table 4. When the tensile test is carried out by using No. 12 test piece for tubes under 8 mm in wall thickness, the minimum value of elongation shall be obtained by reducing 1.5 mm from the elongation value in table 4 at each decrease of 1 mm in wall thickness, and by rounding the result to an integer in accordance with Rule A of JIS Z 8401. The obtained value shall conform to table 5.
Table 4 Mechanical properties
Designa tion of grade |
Tensile strength a) N/mm 2 |
Yield point or proof stress N/mm 2 |
Elongation % | ||||
Outside diameter | |||||||
Under 10 mm | 10 mm or over to and excl. 20 mm | 20 mm or over | All diameters | ||||
Tensile test piece | |||||||
No. 11 test piece | No. 11 test piece | No. 11 test piece or No.12 test piece | No.4 test piece | No.14A test piece | |||
Tensile test direction | |||||||
Pararell to tube axis | Pararell to tube axis | Pararell to tube axis | Pararell to tube axis | Pararell to tube axis | |||
STBA12 | 380 min. | 205 min. | 22 min. | 25 min. | 30 min. | 24 min. | 21 min. |
STBA13 | 410 min. | ||||||
STBA20 | |||||||
STBA22 | |||||||
STBA23 | |||||||
STBA24 | |||||||
STBA25 | |||||||
STBA26 | |||||||
NOTE: 1 N/mm 2 = 1 MPa Note a) Exclusively for the heat exchanger tube, the purchaser may, where necessary, designate the maximum value of tensile strength, which shall be obtained by adding 150N/mm 2 to the value given in this table. |
Table 5 Minimum elongation values for No. 12 test piece taken from tubes under 8 mm in wall thickness (parallel to tube axis)
Unit: %
Wall thickness | Over 1 mm up to and incl. 2 mm | Over 2 mm up to and incl. 3 mm | Over 3 mm up to and incl. 4 mm | Over 4 mm up to and incl. 5 mm | Over 5 mm up to and incl. 6 mm | Over 6 mm up to and incl. 7 mm | Over 7 mm to and excl. 8 mm |
Elongation | 21 min. | 22 min. | 24 min. | 26 min. | 27 min. | 28 min. | 30 min. |
6.2 Flattening resistance
Tubes shall be tested in accordance with 10.2.4, and the test piece shall be free from cracks. In this case, the distance H between the two flat plates shall be obtained by formula (1).
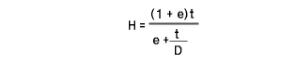
where,
H: distance between flat plates (mm)
t: wall thickness of tube (mm)
D: outside diameter of tube (mm)
e: constant 0.08
NOTE: For flattening test, see 10.2.4.
6.3 Flaring resistance
Tubes shall be tested in accordance with 10.2.5, and they shall be free from cracks when flared into a trumpet shape until the outside diameter becomes 1.14 times the original outside diameter. The flaring resistance for tubes over 101.6 mm in outside diameter shall apply only upon the requirement from the purchaser.
NOTE: For flaring test, see 10.2.5 .
6.3Reverse flattening resistance
The electric resistance welded steel tubes, when tested in accordance with 10.2.6 shall be free from cracks on the weld.
Note: For reverse flattening test see 10.2.6
7 Hydraulic test characteristics or nondestructive test characteristics
Tubes shall be tested in accordance with 10.3, and the hydraulic test characteristics or nondestructive test characteristics shall be as follows. Which of the characteristics is to be tested shall be as specified by the purchaser. If not specified, it shall be left to the
discretion of the manufacturer.
a) Hydraulic test characteristics Hydraulic test characteristics shall be as follows.
1) When the test pressure is specified by the purchaser the tube shall withstand the specified minimum hydraulic test pressure without leakage.If the pressure specified by the purchaser exceeds either the test pressure (p) calculated by formula
(2) or 1O.MPa,the.pressure shall be as agreed between the purchaser and the manufecturer.The.specified test pressure shall be expressed to the. nearest 0.5 MPa for values under 10MPa and.to the nearest 1MPa for values of 10MPa or greater.

p: test pressure (MPa)
t: wall thickness of tube (mm)
D: outside diameter of tube (mm)
s: .60% of the lowest value of yield point or proof stress in table 4 (N/mm2)
2) When the test pressure is not specified by the purchaser the tube shall withstand the minimum ydraulic test pressure (P) calculated by formula(2) (or 10Mpa in the case where the pressure exceeds 10MPa) without leakage.
b)Nondestructive test characteristics Tubes shall be subjected to either the ultrasonic examination or the eddy current examination, and the nondestructive test characteristics shall be as follows. Instead of these tests,other nondestructive test in accordance, with JIS may be performed upon the agreement between the purchaser and the manufacturer in this case the judgement criteria shall be equivalent to or stricter than that applied to in the ultrasonic examination or the. eddy current examination.
NOTE: Other nondestructive tests in accordance with JIS include JIS G 0586,etc.
1) For the ultrasonic examination characteristics, no signal shall be equivalent to or greater than the signal from the reference standard of reference sample of category UD specified in JIS G 0582.
2) For the eddy.current examination characteristics,no signal shall be equivelent to or greater than the signal from the reference standard of reference sample of category EY specified in JIS G 0583.
8 Dimensions, mass and dimensional tolerances
8.1 Dimensions and unit mass
The outside diameter, wall thickness and unit mass of tubes shall be as given in table 6. Dimensions not specified in table 6 may be used upon the agreement between the purchaser and the manufacturer. In this case,the unit mass shall be calculated by the following.formula.assuming 1 cm³ of steel to be 7.85g, and be rounded off to three significant figures in accordance with Rule A of JIS Z 8401.The value over 1000kg/m shall be rounded off to an integer of four significant figures.
W: unit mass of tube(kg/m)
t: wall thickness of tube(mm)
D: outside diameter of tube(mm
0.02466 :conversion coefficient of unit to obtain W
NOTE: The unit mass in table 6 is obtained as above.
Table 6 Dimension and unit mass of alloy steel tubes for boiler and heat exchanger
Unit: kg/m
1.2 | 1.6 | 2.0 | 2.3 | 2.6 | 2.9 | 3.2 | 3.5 | 4.0 | |
15.9 | 0.435 | 0.564 | 0.686 | 0.771 | 0.853 | 0.930 | |||
19.0 | 0.527 | 0.687 | 0.838 | 0.947 | 1.05 | 1.15 | |||
21.7 | 0.607 | 0.793 | 0.972 | 1.10 | 1.22 | 1.34 | 1.46 | ||
25.4 | 0.716 | 0.939 | 1.15 | 1.31 | 1.46 | 1.61 | 1.75 | 1.89 | |
27.2 | 0.769 | 1.01 | 1.24 | 1.41 | 1.58 | 1.74 | 1.89 | 2.05 | 2.29 |
31.8 | 0.906 | 1.19 | 1.47 | 1.67 | 1.87 | 2.07 | 2.26 | 2.44 | 2.74 |
34.0 | 1.28 | 1.58 | 1.80 | 2.01 | 2.22 | 2.43 | 2.63 | 2.96 | |
38.1 | 1.44 | 1.78 | 2.03 | 2.28 | 2.52 | 2.75 | 2.99 | 3.36 | |
42.7 | 2.01 | 2.29 | 2.57 | 2.85 | 3.12 | 3.38 | 3.82 | ||
45.0 | 2.12 | 2.42 | 2.72 | 3.01 | 3.30 | 3.58 | 4.04 | ||
48.6 | 2.30 | 2.63 | 2.95 | 3.27 | 3.58 | 3.89 | 4.40 | ||
50.8 | 2.41 | 2.75 | 3.09 | 3.43 | 3.76 | 4.08 | 4.62 | ||
54.0 | 2.56 | 2.93 | 3.30 | 3.65 | 4.01 | 4.36 | 4.93 | ||
57.1 | 2.72 | 3.11 | 3.49 | 3.88 | 4.25 | 4.63 | 5.24 | ||
60.3 | 2.88 | 3.29 | 3.70 | 4.10 | 4.51 | 4.90 | 5.55 | ||
63.5 | 3.47 | 3.90 | 4.33 | 4.76 | 5.18 | 5.87 | |||
65.0 | 3.56 | 4.00 | 4.44 | 4.88 | 5.31 | 6.02 | |||
70.0 | 3.84 | 4.32 | 4.80 | 5.27 | 5.74 | 6.51 | |||
76.2 | 4.19 | 4.72 | 5.24 | 5.76 | 6.27 | 7.12 | |||
82.6 | 6.27 | 6.83 | 7.75 | ||||||
88.9 | 6.76 | 7.37 | 8.37 | ||||||
101.6 | 8.47 | 9.63 | |||||||
114.3 | 10.9 | ||||||||
127.0 | 12.1 | ||||||||
139.8 |
4.5 | 5.0 | 5.5 | 6.0 | 6.5 | 7.0 | 8.0 | 9.5 | 11.0 | 12.5 | |
15.9 | ||||||||||
19.0 | ||||||||||
21.7 | ||||||||||
25.4 | ||||||||||
27.2 | ||||||||||
31.8 | 3.03 | |||||||||
34.0 | 3.27 | 3.58 | ||||||||
38.1 | 3.73 | 4.08 | 4.42 | |||||||
42.7 | 4.24 | 4.65 | 5.05 | 5.43 | ||||||
45.0 | 4.49 | 4.93 | 5.36 | 5.77 | 6.17 | |||||
48.6 | 4.89 | 5.38 | 5.85 | 6.30 | 6.75 | 7.18 | ||||
50.8 | 5.14 | 5.65 | 6.14 | 6.63 | 7.10 | 7.56 | 8.44 | 9.68 | 10.8 | 11.8 |
54.0 | 5.49 | 6.04 | 6.58 | 7.10 | 7.61 | 8.11 | 9.07 | 10.4 | 11.7 | 12.8 |
57.1 | 5.84 | 6.42 | 7.00 | 7.56 | 8.11 | 8.65 | 9.69 | 11.2 | 12.5 | 13.7 |
60.3 | 6.19 | 6.82 | 7.43 | 8.03 | 8.62 | 9.20 | 10.3 | 11.9 | 13.4 | 14.7 |
63.5 | 6.55 | 7.21 | 7.87 | 8.51 | 9.14 | 9.75 | 10.9 | 12.7 | 14.2 | 15.7 |
65.0 | 6.71 | 7.40 | 8.07 | 8.73 | 9.38 | 10.0 | 11.2 | 13.0 | 14.6 | 16.2 |
70.0 | 7.27 | 8.01 | 8.75 | 9.47 | 10.2 | 10.9 | 12.2 | 14.2 | 16.0 | 17.7 |
76.2 | 7.96 | 8.78 | 9.59 | 10.4 | 11.2 | 11.9 | 13.5 | 15.6 | 17.7 | 19.6 |
82.6 | 8.67 | 9.57 | 10.5 | 11.3 | 12.2 | 13.1 | 14.7 | 17.1 | 19.4 | 21.6 |
88.9 | 9.37 | 10.3 | 11.3 | 12.3 | 13.2 | 14.1 | 16.0 | 18.6 | 21.1 | 23.6 |
101.6 | 10.8 | 11.9 | 13.0 | 14.1 | 15.2 | 16.3 | 18.5 | 21.6 | 24.6 | 27.5 |
114.3 | 12.2 | 13.5 | 14.8 | 16.0 | 17.3 | 18.5 | 21.0 | 24.6 | 28.0 | 31.4 |
127.0 | 13.6 | 15.0 | 16.5 | 17.9 | 19.3 | 20.7 | 23.5 | 27.5 | 31.5 | 35.3 |
139.8 | 18.2 | 19.8 | 21.4 | 22.9 | 26.0 | 30.5 | 34.9 | 39.2 |
8.2 Dimensional tolerances
Dimensional tolerances of tubes shall be as follows.
a) The tolerances on the outside diameter of tubes shall be as given in table 7.
b) The tolerances on the wall thickness and wall thickness deviation of tubes shall be as given in table 8.
c) The tolerances on the length of tubes shall be as given in table 9.
(a)The tolerance on the outside diameter of the tube
Table 7 Tolerances on Outside Diameter Unit: mm
Division of outside diameter | Tolerances on outside diamete | |||
Hot finished seamless steel tube | Cold finished seamless steel tube | Electric resistance welded steel tube other than cold finished | Cold finished electric resistance welded steel tube | |
Under 25 |
+0.4 -0.8 |
【0.10 | 【1.5 | 【0.10 |
25 or over to and excl. 40 | 【0.15 | 【0.20 | 【0.15 | |
40or over to and excl. 50 | 【0.20 | 【0.25 | 【0.20 | |
50 or over to and excl 60 | 【0.25 | 【0.30 | 【0.25 | |
60 or over to and excl. 80 | 【0.30 | 【0.40 | 【0.30 | |
80 or over to and excl. 100 | 【0.40 | +0.40 | 【0.40 | |
-0.60 | ||||
100 or over to and excl.12 |
+0.4 -1.2 |
+0.40 -0.60 |
+0.40 -0.80 |
+0.40 |
-0.60 | ||||
120 or over to and excl.160 |
+0.40 -0.80 |
+0.40 -1.00 |
+0.40 | |
-0.80 | ||||
160 or over to and excl.200 | +0.4 | +0.40 | +0.40 | +0.40 |
-1.8 | -1.20 | -1.20 | -1.20 | |
200 or over | +0.4 | +0.40 | +0.40 | +0.40 |
-2.4 | -1.60 | -1.60 | -1.60 |
(b)Tolerances on Wall Thickness and on Thickness Deviation
Table 8 Tolerances on Wall Thickness
Tolerances |
Division of wall thickness (mm) |
Division of method of manufacture | Hot finished seamless steel tube | Cold finished seamless steel tube | Electric resistance welded steel tube | |||
Division of outside diameter (mm) | Under 100 | 100 or over | Under 40 | 40 or over | Under 40 | 40 or over | ||
Tolerances on wall thickness % | Under 2 | --- | --- | +0.4mm |
+22 0 |
+0.3 |
+18 0 |
|
0 | 0 | |||||||
2 or over to and excl. 2.4 | +40 | --- |
+20 0 |
+18 0 |
||||
0 | ||||||||
2.4 or over to or excl. 3.8 | +35 | +35 | ||||||
0 | 0 | |||||||
3.8 or over to or excl. 4.6 | +33 | +33 | ||||||
0 | 0 | |||||||
4.6 or over | +28 | +28 | ||||||
0 | 0 | |||||||
Tolerances on thickness disparity % |
--- | Within 22.8 of wall thickness | --- | --- |
(c)The Tolerance on length of the tube
Table 9 Tolerances on the length
Division | Tolerance on length | ||
50 mm or under in outside diameter |
7 m or under in length | +0.7 mm | |
0 | |||
Over 7 m in length | Add 3 mm to the plus side permissible deviation given above for each increase of 3m or its fraction in length. However, the maximum value shall be 15 mm. | ||
Over 50 mm in outside diameter |
7 m or under in length | +10mm | |
0 | |||
Over 7 m in length | Add 3 mm to the plus side permissible deviation given above for each increase of 3m or its fraction in length. However, the maximum value shall be 15mm. |
9 Appearance
The appearance of tubes shall be as follows.
a) The tube shall be practically straight, and the both ends shall be practically perpendicular to the tube axis.
b) The inside and outside surfaces of the tube shall be finished well without defects detrimental to use. In the case of electric resistance welded steel tube, the swelling of inside surface of the weld shall be 0.25 mm or under. The purchaser may specify the inside swelling to be 0.15 mm or less for tubes of 50.8 mm or under in outside diameter and 3.5 mm or under in wall thickness.
c) The surface of the tube may be repaired by grinding, machining or other methods,provided that the wall thickness after repairing still satisfies the specified tolerance on thickness.
d) The surface of repaired part shall be smooth along the contour of the tube.
10 Tests
10.1 Chemical analysis
10.1.1 General matters of chemical analysis and sampling method
General matters of chemical analysis and sampling method of analytical sample shall be in accordance with clause 8 of JIS G 0404. The sampling method when the product analysis is required by the purchaser shall be in accordance with clause 4 of JIS G 0321.
10.1.2 Analytical method
Heat analysis shall be in accordance with JIS G 0320. Product analysis shall be in accordance with JIS G 0321.
10.2 Mechanical test
10.2.1 General
General matters of mechanical test shall be in accordance with clauses 7 and 9 of JIS G 0404. The sampling method for mechanical tests in 7.6 of JIS G 0404 shall be in accordance with Class A.
10.2.2 Sampling method and number of test pieces
For the sampling method and number of test pieces, one sample shall be taken from each unit of 50 tubes or its fraction of the same dimension and the simultaneous heat treatment. From each sample thus obtained, one tensile test piece, one flattening test piece and one flaring test piece shall be taken. The "same dimension" refers to the same outside diameter and the same wall thickness. The "simultaneous heat treatment" in the case of using continuous furnace refers to a continuous heat treatment performed under same heat treatment conditions. Therefore, if the continuous furnace is stopped, the tubes do not belong to the simultaneous heat treatment. When all tubes of the same dimension to be tested belong to the same heat, the same heat treatment conditions may be applied instead of the simultaneous heat treatment.
In addition, for electric resistance welded steel tubes, one sample shall be taken from each unit of 100 tubes or its fraction of the same dimensions and the simultaneous heat treatment. From each sample thus obtained, one reverse flattening test piece shall be taken.
10.2.3 Tensile test
The tensile test piece and tensile test method shall be as follows.
a) Test piece Tensile test piece shall be one of No. 11, No. 12 (No. 12A, No. 12B and No. 12C), No. 14A or No.4 test pieces specified in JIS Z 2241, taken in parallel to the tube axis. The sampling position in thickness direction of No. 14A or No.4 test pieces used for bars shall be in accordance with A.7 of JIS G 0416. No.4 test piece shall have a diameter of 14 mm (gauge length 50 mm).
In the case of obtaining a tensile test piece from an electric resistance welded steel tube, No. 12 test piece shall be taken from a position without any weld.
b) Test method The test method shall be in accordance with JIS Z 2241.
10.2.4 Flattening test
The flattening test piece and the test method shall be as follows.
The flattening test of seamless steel tubes may be omitted unless otherwise specified by the purchaser 1 ).
Note 1) This means that the flattening test may be omitted at the discretion of the manufacturer, but only on the precondition that the flattening resistance of the tube satisfies the specification.
a) Test piece The test piece shall have a length of 50 mm or over. For tubes of wall thickness 15 % or over of the outside diameter, a C-shape test piece made by removing a part of the circumference of a ring-shaped test piece may be used.
b) Test method The test piece shall be placed at ordinary temperature between two flat plates and flattened by compression until the distance Hbetween the plates is decreased to the value obtained by formula (1) in 6.2 or less, and then examined for cracks. In the case of electric resistance welded steel tubes, however, the test piece shall be placed, as shown in figure 1, so that the line connecting the centre of the tube and the weld is perpendicular to the direction of compression. A C-shape test piece shall be placed as shown in figure 2.
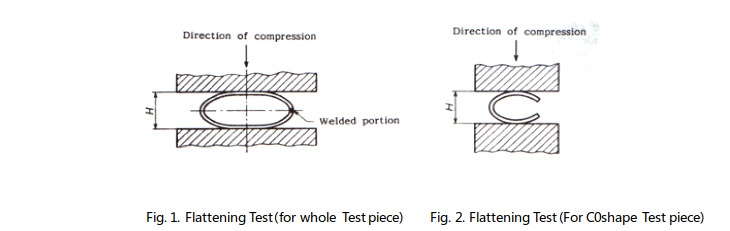
10.2.5 Flaring test
TheFlaring test piece and the test method shall be as follows.
The flaring test of seamless steel tubes may be omitted unless otherwise specified by the purchaser 2).
Note 2) This means that the flaring test may be omitted at the discretion of the manufacturer, but only on the precondition that the flaring resistance of the tube satisfies the specification.
a) Test piece The test piece shall have a length suitable for the test.
b) Test method The test piece shall be flared at one of the tube ends at ordinary temperature into a trumpet shape and to at least the size specified in 6.3 with conical tool forming an angle of 60°, and examined for any cracks.
10.2.6 Reverse flattening test
The reverse flattening test piece and the test method shall be as follows.
When the flaring test is carried out, the reverse flattening test may be omitted unless otherwise specified 3).
Note 3) This means that the reverse flattening test may be omitted at the discretion of the manufacturer, but only on the precondition that the reverse flattening resistance of the tube satisfies the specification.
a) Test piece A length of 100 mm shall be cut off from one end of the tube to prepare a sample. This sample shall be split in half by cutting at positions that are displaced 90° circumferentially from the weld line to its both sides, and one of the split halves which contains the weld shall be used as a test piece.
b) Test method The test piece shall be opened up and flattened by positioning the weld line at the top, and then examined for any cracks in the weld.
10.3 Hydraulic test or nondestructive test
The hydraulic test or nondestructive test shall be as follows.
a) Frequency of test The hydraulic test or nondestructive test shall be carried out for each one of tubes.
b) Test method The hydraulic test or nondestructive test shall be as follows.
1) Hydraulic test The tube shall be held under at least the minimum hydraulic test pressure specified in 7 a) for at least 5 s, and then examined if it endures the pressure without leakage.
2) Nondestructive test The test method shall be as follows. Other nondestructive tests in accordance with JIS, when performed, shall be as agreed between the purchaser and the manufacturer.
2.1) The ultrasonic examination shall be in accordance with JIS G 0582. The test may be conducted by a category of reference standard stricter than category UD.
2.2) The eddy current examination shall be in accordance with JIS G 0583. The test may be conducted by a category of reference standard stricter than category EY.
11 Inspection and re-inspection
11.1 Inspection
The inspection shall be as follows.
a) General matters of inspection shall be in accordance with JIS G 0404.
b) The chemical composition shall conform to clause 5.
c) The mechanical properties shall conform to clause 6.
d) The hydraulic test characteristics or nondestructive test characteristics shall conform to clause 7.
e) The dimensions shall conform to clause 8.
f )The appearance shall conform to clause 9.
In the case where a part or all of the special quality requirements in Annex JA are applied upon the agreement.between the purchaser and the manufacturer,and or in the case where U-bend tubes in Annex JB are specified,the inspection results shall conform to the relevant requirements.
11.2 Re-inspection
Tubes which failed mechanical test may be further evaluated for acceptance by conducting a retest specified in 9.8 of JIS G 0404.
12.Marking
The tubes which have passed the inspection shall be marked with the following items on each tube. However, the order of arranging the items is not specified.
Further, in the case of either smaller tubes or a request from the purchaser, the tubes may be bundled together and marked by a suitable method on each bundle.
Moreover, when approved by the purchaser, part of items may be omitted.
(1) Symbol of class
(2) Symbol representing the method of manufacture (³)
(3) Dimensions
(4) Manufacturer's name or its abbreviation
(5) Symbol representing the designation of special quality requirements: Z
Note ( 2 )
Symbols representing the methods of manufacture shall be as follows:
However, the sign - may be replaced by a blank.
Hot finished seamless steel tube - S - H
Cold finished seamless steel tube - S -C
Electric resistance welded steel tube other than hot finished and cold finished - E - G
Hot finished electric resistance welded steel tube - E - H
Cold finished electric resistance welded steel tube - E - C
13 .Test report
The manufacturer shall submit an inspection document to the purchaser unless otherwise specified. The test report shall be in accordance with clause 13 of JIS G 0404.
The type of the inspection document shall be the standard designation 3.1 in table 1 of JIS G 0415, unless otherwise specified at the time of ordering.
If any alloy elements not specified in table 3 are intentionally added, the content of the added alloy elements shall be appended to the inspection document.
Annex JA (normative) Special quality requirements
This Annex specifies the special quality requirements. The special quality requirements shall be applied to a part of or all items on straight tubes upon the agreement between the purchaser and the manufacturer.
JA.1 Hardness (ZI) 1)
The hardness shall be as follows.
a) The hardness of tubes shall be as given in table JA.1.
Table JA.l Hardness
b) The sampling method and the number of test pieces shall be in accordance with that of the tensile test in 10.2.2.
c) An adequate length shall be cut off from one end of a tube to prepare a test piece.
d) The test method shall be in accordance with JIS Z 2245. The hardness of cross section or inside surface of the test piece shall be measured at three points on each test piece.
Tubes of 2 mm or under in wall thickness shall not be tested. For the electric resistance welded steel tubes, the test shall be conducted in the portion without any weld and heat-affected zone.
e) The hardness of tubes shall conform to table JA.1.
:0 Retest Tubes may be further evaluated for acceptance by conducting a retest specified in 9.8 of JIS G 0404.
Note 1) The hardness can be designated as Z1 on transaction of tubes.
JA.2 Yield point or proof stress in elevated temperature tensile test (Z2) 2)
The yield point or proof stress in elevated temperature tensile test shall be as follows.
a) Yield point or proof stress value and the test temperature in the elevated temperature tensile test of tubes shall be as agreed between the purchaser and the manufacturer.
b) For the sampling method and number of test pieces, one sample shall be taken from each unit of tubes belonging to the same heat. From each sample thus obtained, one test piece shall be taken for each test temperature.
c) Test piece and test method shall be in accordance with JIS G 0567.
If taking a test piece as specified in JIS G 0567 is impracticable, the shape of the test piece shall be as agreed between the purchaser and the manufacturer.
Note 2) The specification of the yield point or proof stress in elevated temperature tensile test can be designated as Z2 on transaction of tubes.
JA.3 Ultrasonic examination and inspection (Z3) 3)
The ultrasonic examination and inspection shall be as follows.
a) The criteria of the working sensitivity in the ultrasonic examination shall be category DA or DC as defined in JIS G 0582, and no signal shall be equivalent to or greater than the signal from the reference standard of the reference sample.
b) The method of ultrasonic examination shall be in accordance with JIS G 0582.
c) The ultrasonic inspection shall be performed for each tube and the results shall conform to the requirements specified in a).
Note 3) The specification of the ultrasonic examination can be designated as Z3 on transaction of tubes.
JA.4 Eddy current examination and inspection (Z4) 4)
The eddy current examination and inspection shall be as follows.
a) The criteria of the working sensitivity in the eddy current examination shall be category ED, EV, EW or EX as defined in JIS G 0583, and no signal shall be equivalent to or greater than the signal from the reference standard of the reference sample.
b) The method of the eddy current examination shall be in accordance with JIS G 0583.
c) The eddy current examination shall be performed for each tube and the results shall conform to the requirements specified in a).
Note 4) The specification of the eddy current examination can be designated as Z4 on transaction of tubes.
Annex JB (normative)
U-bend tubes
This Annex specifies the U-bend tubes. When required by the purchaser in addition to the items specified in the text, the requirements given in this Annex shall be applied by the manufacturer.
JB.l Manufacturing method
The manufacturing method shall be as follows (see figure JB.l).
a) The U-bend tubes shall be made by cold-bending process, and the bending radius shall be at least 1.5 times the outside diameter of the tube.
b) The bent portion of the tube shall not be heat treated in general. When required by the purchaser, the heat treatment may be agreed between the purchaser and the manufacturer.
JB.2 Appearance
The bent portion shall be free from defects detrimental to practical use.
JB.3 Dimensional tolerances on U-bend tubes
The outside diameter variation of bent portion, the wall thickness reduction rate and the tolerance on pitch (p) or P (p + Dn) shall be as given in table JB.1. The tolerance on length after bending shall be as given in table JB.2.
JB.4 Measurement of dimensions ofU-bend tubes
From an unit of tubes of the same dimension that have been bent at the same time,one sample product with the smallest bending radius shall be taken. The outside diameters of the tube shall be measured in the two circumferential directions (minor axis side and major axis side) at 90° from the bent portion (dimension Ds in figure JB.l) to determine the variation of the outside diameter. Also, the wall thicknesses of the tube in that position shall be measured at four points on the circumference, to obtain the wall thickness reduction rate as the minimum value of the four measurements.
JB.5 Hydraulic test characteristics
The manufacturer may perform the hydraulic test in 10.3 b) 1) by using aU-bend tube instead of a straight tube. In this case, the hydraulic test characteristics of the U-bend tube shall conform to 7 a).