Degreasing process of stainless steel oxygen pipeline
Chemical cleaning and degreasing process of stainless steel oxygen pipeline
The cleaning steps of the stainless steel oxygen pipeline are as follows: water flushing→manual wiping and degreasing→water flushing→compressed air (or nitrogen) purge
Cleaning and degreasing method
The first step: water rinse
1. The purpose of water washing is to remove ash, silt, detached metal oxides and other loose dirt in the pipeline.
2. When flushing, use small high-pressure water cleaning equipment to flush, and the pressure is controlled at about 0.6Mpa to ensure that the impurities inside the pipeline are flushed clean.
Step 2: Manual wiping and degreasing
1. The purpose of manual wiping and degreasing is to remove all kinds of oil, graphite, anti-rust oil and other organic substances in the pipeline to ensure that the pipeline is clean and clean during installation and meet the requirements of equipment operation.
2. Pour the cleaning and degreasing mixture into the cleaning basin, add it in proportion, mix it evenly and use it, and wipe it repeatedly.
3. During the cleaning process, the cleanliness of the degreasing cleaning fluid should be monitored. If the color of the degreasing cleaning fluid becomes dirty, the existing degreasing fluid should be drained and the degreasing cleaning fluid should be reconfigured.
4. The required agent and concentration
1), trichloroethylene above 98%
2), surface active agent 0.2%
3) Penetrant 0.2%
5. Testing items and frequency
Check the cleanliness of the degreasing cleaning fluid
6. Process conditions and parameters
1), temperature, normal temperature
2), time 1-2 hours
The third step: water rinse
The purpose of water flushing after degreasing is to flush the degreasing residue in the pipeline. After the degreasing of the pipeline is completed, flush with a large amount of water. When the flushing water flowing out of the pipeline is clean, the water flushing can be ended.
The fourth step: compressed air (or nitrogen) purge
Use oil-free compressed air (or nitrogen) to blow, dry the inside of the pipe and use a clean plastic cloth to wrap the pipe mouth or parts and seal it, so as to ensure the cleanness of the pipe and avoid secondary pollution.
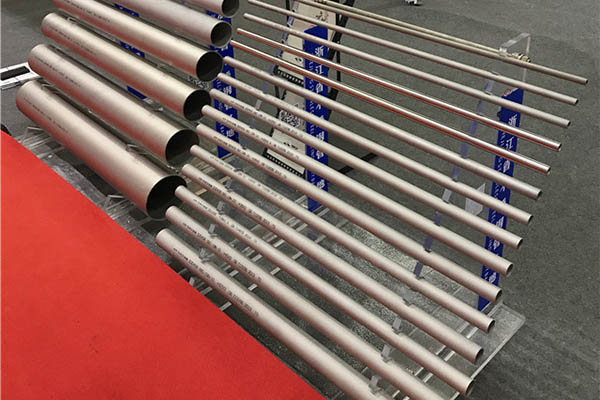
Chemical cleaning waste liquid treatment
The cleaning waste after the chemical cleaning mainly includes water washing waste, degreasing waste, pickling waste, rinsing waste and neutralization and passivation waste.
1. Disposal of waste liquid from water flushing
Because the waste liquid of the water washing part mainly contains some welding slag, rust and some other impurities. This part of the waste liquid has no substances harmful to the environment and can be directly discharged into the sewage discharge well designated by Party A.
2. Degreasing waste liquid, pickling waste liquid, rinsing waste liquid and neutralization passivation waste liquid should be neutralized according to the national three-level discharge standard. After the neutralization treatment is completed, it shall be discharged into the sewage discharge well designated by Party A.
Chemical cleaning quality standards
After the pipeline is cleaned, the following requirements should be met:
1. Check the inner wall of the pipeline with ultraviolet light with a wavelength of 320~380nm, and there should be no grease fluorescence.
2. Wipe the inner wall of the pipe with clean and dry white filter paper. There should be no traces of oil stains on the paper.
3. Other relevant technical indicators proposed by the client.
Construction requirements and safety requirements
1. Construction requirements
1). Special training and technical clarification must be carried out before cleaning personnel work.
2) Operators should be familiar with the cleaning plan and cleaning plan, and be able to complete temporary piping in accordance with the cleaning requirements.
3). Operators must be familiar with the maintenance of the pump and emergency handling methods.
4). Chemical cleaning operators must understand the performance characteristics, use requirements and storage methods of various chemicals.
5) During the cleaning process, the system shall be inspected every half an hour, and the high point shall be vented regularly and the low point coagulation shall be discharged according to the requirements.
6) The cleaning solution is the key to chemical cleaning and degreasing, and it must be reasonably configured according to the pipe material, the degree of rust, and the nature of the oil.
7) Before the cleaning operation, the temporary piping system circuit shall be subjected to a pressure test of not less than 0.1MPa, and the cleaning operation shall be carried out after confirming that there is no leakage.
2. Safety requirements
1. During the cleaning process, all operators must wear corresponding labor protection supplies to ensure personal safety.
2. Carry out storage and transportation in accordance with regulations. Do not mix acid and alkali. Use rubber pads of more than 5mm for on-site storage. Use “dangerous” and other eye-catching signs for the storage of medicines.
3. During the cleaning process, if workers accidentally touch the cleaning fluid, they should rinse with clean water first, and then send them to the hospital for further treatment in time.
Finished product protection
1. Disassembly and installation of cleaning pipes and temporary piping shall not change the shape of the original piping.
2. In the cleaning process, a dedicated instrument worker should be equipped to be responsible for the installation and disassembly of the temperature and pressure measurement components, instruments, control valves, etc. in the on-site pipeline.
3. During the cleaning process, the disassembled pipeline components should be properly kept before and after cleaning to avoid damage, loss or contamination.
4. After cleaning, the pipeline components should be reset quickly and timely, and each circuit should not exceed 3 hours, and the seals of the reset interface should be installed and clean.
5. After the carbon steel pipe system is reset, the system should be filled with nitrogen in time, and the air in the system should be safely converted. Each system has three pressure gauges to detect the nitrogen seal pressure. In order to ensure the effect of nitrogen sealing, a dedicated person should be assigned to perform nitrogen sealing protection inspections, and the pressure of the nitrogen sealing should be guaranteed to be 0.07-0.1MPa.
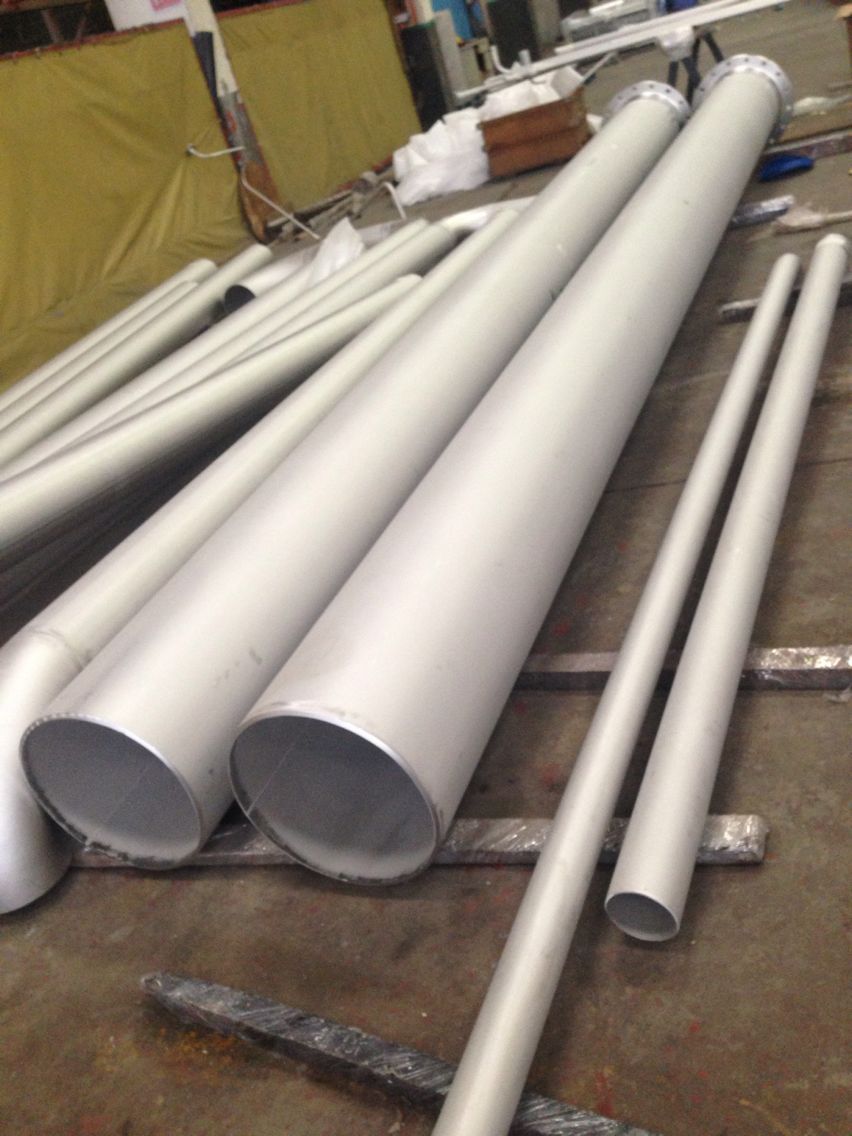
Quality records
This process standard should have the following records
1. Process handover record;
2. Pipeline degreasing and pickling records;
3. Pipeline cleaning records.
Concluding remarks
With the increasing level of industrialization in my country and the vigorous development of coal chemical projects in recent years, more and more oxygen pipelines appear in industrial construction projects. Most of the oxygen pipelines transport oxygen with a purity greater than 99.99%. The pressure is high and the flow rate is fast. If the internal cleanliness of the oxygen pipeline cannot be ensured, the sparks generated by the friction between the debris in the pipeline and the pipe wall can easily cause the oxygen pipeline to deflagrate. Explosion accidents cause greater harm to enterprise property and personal safety. The oxygen pipeline chemical cleaning and degreasing process standardizes the oxygen pipeline cleaning and degreasing construction process, greatly improves the internal cleanliness of the oxygen pipeline, and is a reliable guarantee for the safe and efficient operation of the oxygen pipeline. It is worthy of every chemical construction enterprise's attention and promotion.
References
1. "Quality Standard for Chemical Cleaning of Industrial Equipment" HG/T 2387-2007;
2. "Code for Construction and Acceptance of Degreasing Engineering" HG 20202-2014;
3. Construction drawings and technical documents provided by China Chengda Design Institute.